塑胶模具设计经验及注意事项大全及使用材料
1.滑块导轨的高至少要为滑块高的1/3,以保証滑块稳定以及滑动顺畅。
2.有滑动摩擦的位置注意开设润滑槽,为了防止润滑油外流,不宜把槽开成“开式”,而应该为“封闭式”,一般可以用单片刀在铣床上直接铣出。
3.固定模仁的型腔,对小模一般用线割,这样可以提高模具的精度;而较大模的模腔一般铣削的形式加工出来,加工时注意其垂直度,并且为了防止装配时,模仁不到位,模框的四周应该用铣刀铣深0.2。
4.入子与模仁,模仁与模仁,模仁与模框的相互穿插一般要加1°的斜度,以防装配时碰伤。
5.入子的靠位部分长度公差为-0.02,大小公差为-0.10,模仁相对应的靠位公差为+0.02。
6.有C 角的入子更底端到C 角部位的公差为+0.01,以防跑毛边。
7. 本体模具的主体部分用NAK80 的材料,入子、梢等用SKH9、SKH51(材料处理:室化处理,也可以不要)的材料,必要时可以使用VIKING 材料。
8.画好部品之后,应先定滑块的位置、大小,防止发生干涉、及强度不够的现象,然后才定模仁寸法。
9.入子大小公差设为-0.01,模仁上入子孔对应的公差为+0.01。
10.模仁上的线割方孔尖角部分用R0.20 过度,对应的入子部分也为R0.20,以对应线切割时的线径影响,同时可以防止尖角部分磨损,而产生益边。
11.与定位珠相对应的小凹坑寸法一般为底径φ3 夹角90°-120°的圆锥孔。
12.固定侧的拔模角应该大于可动侧,以便离型留在可动侧;而且可以防止部品变形,尤其是壁薄,件长容易变形的零件,固定侧对它的拉力不均容易使部品翘曲,或留在固定侧。
13.对于侧面抽芯力大而部品精度要求又严的零件,更好采用二次抽芯结构。
14.斜梢的斜度+2°=压紧块的斜度(一般为18°或20°或22°).
15.模具组立时,应该养成如下习惯:
a.用空气枪清理模仁、模腔、入子、流道板、分模面的表面。
b.装配前用油石打光模仁、模腔、入子、分模面的表面,以便装配时顺tang。
c.注意清角,以防干涉、碰伤。
d.装配前应该考虑后面的工作如何进行。
16.大模具模仁的侧面压紧块应该设计成锁紧后底于分模面0.5-1.0mm,以防干涉。
17. PC+GF20 收缩率3/1000
18.POM 收缩率正常为20/1000,但有时局部会达30/1000。
19.为防止潜伏式浇口在部品顶出时刮伤部品,在流道离潜伏式浇口2-4mm 处增加一锲形块,高约为流道一半,夹角为单边10°,供顶出时折断浇口。
20.主流道拉料井,采用深8-10mm,夹角为单边10°,顶径为流道宽的倒圆锥;这样的好处是可防止单边磨成锲形的拉料在顶出时勾住流道,造成离型不良。
21.开闭器有两种:
1.橡胶制成,靠中心的螺杆调节变形量,来调节拉力。
2.用弹簧钢制成。其作用都为:延迟可动侧与固定侧的开模时间,应用于小水口模。
22.为了确保模具的顶针和斜销是否复位,有些模具安装了早回机构(母的装在108 板上,公的装在102 板上,公的类似于顶针,底部用无头螺钉堵住,一般布置两个)或微动开关(在108 和109 板[装电器元件]之间)。
23.考虑注塑机装夹模具时的螺杆长度,需要注意上下固定板的厚度,必要时四个角应该铣低一些,同时,为了提高安全性,上下固定板上可以根据注塑机上孔的位置,钻四个螺栓孔。
24.斜销的成型端有一段直面,一般长4-6mm,为了在顶出时斜销在107 与108板间滑动顺烫底部应该倒0.5mm-1mm 的R 角。
25.需要咬花的外观品,拔模斜度的设计需要考虑咬花的程度,以免造成外观拉伤。有些突出部位,考虑咬花后截面会变大,实际加工时应该单边小0.02-0.03。
26.考虑固定侧与可动侧合模会形成断差,固定側比可动侧单边小0.03-0.05。
27.有滑块的模具中,有时需要在滑块上的滑块与压紧块相靠的斜面开设油沟;此外,如果不影响成形的前提下,在模板上表面开设油沟比在滑块底部开设油沟加工效率更高。
28.不应该把分型面选在表面有要求的位置。
29.加纤的收缩率为流动方向小千分之1-2,垂直于流动方向大;不加纤的则正好相反。
30.齿顶圆的收缩率比齿根圆的收缩率小千分之1-2。
31.模具在使用一段时间后,需要进行型修,修模仁的过程中,尽量不要用油石,因为多次使用油石会使模具变形;更好用削好的软木或软竹筷。
32.有滑块的模具中,#102 与#103 板之间应该加四个支撑拄。
33.成形里面夹有入子外面包有模仁的部品时,要考虑二次抽芯机构,以免脱模困难,造成部品损伤;如果入子在固定侧或滑块上,常常先抽入子;如果入子在可动侧,又与固定侧靠破,可以把入子的沉孔做深些,顶出时先把部品顶出,再脱出入子。如不靠破,则应先脱入子,则应该变更相应的模具结构。
34.固定侧与可动侧之间的靠破面如果为非垂直开模方向的平面,则应该设计成斜面,以减少因摩损而形成飞边的可能,同时也使靠破时形成预压,加强两个面的贴合,设计时长度方向应该设计成+0.02 的正公差,但是应该注意的是当固定侧与可动侧有脱模斜度时,要小心考虑因固定侧与可动侧脱模斜度方向相反,在靠破的斜面处会形成与部品设计原图不符的接痕,考虑不周还会形成难以消除的毛边或断插。
35.当固定侧需要咬花时,固定侧的外形尺寸应该根据咬花程度,设计时单边小0.03-0.05mm。
36. 电极的抛光一般用1000 的砂纸精抛,但外观电极需要用1200 以上的砂纸精抛;模仁的抛光用1500,但要求有镜面的则要用3000 的砂纸,更后用钻石膏和脱脂棉来精抛。配入子时,先用400 的砂纸,再用800 的砂纸,不过,日本模具中入子好象用了1000-1200 的砂纸进行抛光过。
37.塑胶齿轮成形后,对齿轮参数的测量主要齿顶圆和跨齿厚,如果两齿轮靠得太紧,或太松都会影响到传动性;跨齿厚的测量有专门的测量仪器。
38.模具设计中,如果部品的肉厚不均匀,而部品的浇口均匀分布,则容易产生浇注不均的现象。比如,田晶东的0004 模具。
39.用PC+30GF 制造的齿轮,虽然在成形的尺寸方面比较好,一般可以一模四件,但是其刚性,耐磨性等不如PBT+GF30,因此,虽然PBT 在成形方面尺寸不易控制,只能一模两件,但是象Olympus 这样注重品质的厂家,在品质与成本面前,还是选择了品质。
40.模具设计中,为了不影响部品的使用,常需在部品表面凹进一块,让浇口剪断残余低于部品表面,内凹深度以满足浇口残余低于部品表面的前提下越浅越好,一般为0.3-0.5mm,太深则会影想成形时的尺寸,比如田晶东的0004 模具和易湘成的0026 模具。
41.为了改善部品距离浇口较远端的填充性能,可以在这些部位开设逃气槽,增加入子;这一点,设计前尤其应该考虑的,定结构时,应该有这样一种观念:尽量让流体在模腔内流动时各个部分的压力,温度均恒。
42.部品肉薄,成形困难的模具,如王锋的0001 与0002,通过加大点浇口可提高其成形性能,但是并非越大越好,如果过大,浇口剪断时会从部品上撕下一些肉,形成一个凹坑,同时,部品的取向作用会增大,易变形。因此点浇口以¢0.5-1.2mm 为宜。
43.电火花加工中,放电间隙和加工精度有直接联系(一般认为为3:1)。
44. 大模仁的压紧块斜度为1°、3°、5°
45.为了便于斜销顶出,设计时应该把斜销设计得比正常短0.1-0.3mm,即该部份肉比正常厚0.1-0.3mm。
46.设计模具时首先应该考虑零件的加工工艺,尽量避免使用放电与线割,而要尽量考虑使用铣床和磨床的方式,因为从加工成本、加工精度与加工时间来说,前者都比不上后者,虽然慢走丝线切割的精度不错。
47.设计时应该避免形状简单,但又需大面积的平面放电,既费时,精度又难保证,而且加重钳工的钳配工作量。
48.设计时应该尽量避免阶梯形的又需要面与面相互贴合的上下模仁设计,这样常常难以加工。模具达人微信公众号都是干货!
49.超声波打磨的缺点为容易因为手感把握不准确,而使模具表面形状失真。
50.模具的量产要求为10000-15000/月时,模仁材料为NAK55。
51.好的注塑机可以通过调整参数,进行5 段以上的分段注射,如可以设为段为填满流道;第二段为填满部品的三分之一;第三段为填满部品的二分之一……等等。从而可以通过分析这几种情况下的部品填充情况,来解决注塑中所存在的问题。
52.对一些部品成型困难,或表面有要求,或有些部位精度在前几次试模中尺寸难达要求的模具,试模时考虑使用多级注射成型。
53.注塑机中日本与台湾机都可以进行多级注射成型,但一般来说,台湾机除了能改变注射速度和。。。。。之外,还能改变注射压力。
54.模具的cavity number 的确定因数有:单件部品的成形费用,平均每件部品的模具制作费用,部品精度要求,模具制作难易程度等决定。
55.成型有腐蚀性树脂是模具材料要选择耐腐蚀材料,或在模具表面作防腐处理;成型含玻璃纤维等高强度填充材料的树脂时,模具零件必须有相应的硬度。
56.水管离模仁的距离应大于4mm。
57.如果预估部品成型困难,需要增加成型压力,则设计时要考虑模具的强度,加大模仁的强度,增加支撑柱,并要注意贴合面之间的公差。
58.精密模具设计中不应该考虑强制脱模机构,否则对模具的量产性、部品精度、甚至部品表面有很大的影响。
59.模具设计中,从成本和制造角度来说,尽量避免滑块和斜梢机构。
60.如果铣床加工完后的模仁余量只剩15-20 条,一模两到四件,则即使是清尖角的电极一般一粗一精就可。
61.复杂曲面电极粗电极放时应该X、Y 向预留0。06,Z 向预留0。07 以上,更后再用精电极来加工。
62.尖角、半圆及半球电极的放电需要特别注意。
63.小水口模具的开模行程的确定如下:A.101A 板与102 板脱流道行程计算为:流道长+机械手(40-60mm);B.102 板与103 板脱部品行程计算为:部品+机械手(70mm)
64.象压块、小水口的流道板、模仁等等在模具装配时难以取出的零件,必需钻起吊螺丝孔;不过,有时为了简便起见,可以把对角上的两个锁模螺丝孔钻穿,攻牙攻穿来拧起吊螺钉。
65.要求同心度很好但又不能同时做在固定侧或可动侧的模具,如果模仁的大小允许,固定侧与可动侧应设计有一公一母的圆锥形导向机构,以保证成型时该位置的同心度。如9018、9026、0004、0032 辊筒模具上都加有#251 入子。
66.成型数量大的模具,在模架的选材(可考虑用P20)、滑块的选材(P20)上考虑,同时可以在侧猾块上安装耐模板。
67.用磨床或铣床加工厚度小于5mm,长度大于50,即长厚比大于10,比如斜梢之类的模具零件时,应该注意加工时的变形问题。
68.有时用于放置模仁的模腔太深,而又必需开设冷却环时,如果直接用刀去加工模腔中的冷却槽则刀往往不够长,那么,可以考虑把冷却槽开在模仁的底部,但需要注意的一点是,冷却槽中间的圆柱应比冷却环内径略大,让冷却环不易从冷却槽中掉出。(注意,因为,冷却水是从里面过,设计时应该让冷却环内径和贴紧模壁;如果冷却水是从外面过,设计时应该让冷却环外径和贴紧模壁,这一点千万不要搞反了,否则会造成漏油)
69.冷却水的出、入口温度应尽量小,一般模具控制在5°C 以内,精密模具控制在2°C 以内。
70.水道之间的中心距离一般为水道直径的3~5 倍,水道的外周离模具型腔表面的距离一般为10-15mm。
71.对聚乙烯(PE)等收缩率較大的成型树脂,必需制品收缩大的方向设置冷却回路。
72.模具上有数组冷却回路时,冷却水应首先通入接近主流道的部位。(怎么理解?)
73. 斜梢的材料一般要求比较硬(使用SKH9、或STAVAX),同时为了提高量产性,在斜梢底部(#106 顶针板与#107 顶针固定板)间增加耐磨板(SKS3 材料),厚度与顶针底同厚。模具达人微信公众号都是干货!
74. 一般产品的凹陷量为3%以下,几乎都可以使用强制脱模,如果超过一定范围,在脱模时将使成品产生刮伤甚至破坏的现象。凹陷量也因材料而易,软质材料如PP、NYLON 可达5%,而PC、POM 等只能为2.5~3%之间。
75.滑块的安全距离一般为1.5~5mm。
76.塑料螺纹的根部或顶端部应有一小平面(0.8mm 左右),是为了成型后易脱模,且不易伤害螺纹部分的表面。
77.间隔板的公差一般为+0.1mm,如果模具的压力大则需要加支撑柱,支撑柱的公差一般为+0.02~0.03mm,也就是组立后比间隔板厚0.02~0.03mm,这样考虑的原因是:支撑柱(S45C或S55C)的表面经过淬火比模板硬,使用一段时间后模板会下凹正好补偿该公差。若支撑柱比间隔板薄0.1mm,注塑时的压力使#103 板产生的变形会放大的模仁上,产生不止0.1mm 的弯曲,从而产生毛边。
78. PD613(较优于SKD11)、PD555(较优于SUS 420 J2)与NAK 101(较优于SKD11)等热处理的更大变形量为0.065/50,有高耐磨耗性、高耐腐蚀性、高镜面加工性,适合于加工精密模具。
79.分模面与流道周围常常开设排气槽,对一般模具排气槽的外边一般为0.5mm 深,靠部品侧为0.02mm;而对象相机前后盖本体等精密模具排气槽的外边一般为0.07-0.1mm 深,靠部品侧为0.007-0.01mm。
80.为保证可动侧与固定侧贴合良好,分模面一般比模板高0.02mm;并且常在#103 的四个角上铣C10-20 深0。5-1 的缺口,以保证#102 与#103 不干涉。
81.象聚缩醛(polyacetal)成品尺寸公差是±0.2%左右,模穴数增加1 个公差约增大5%.8 穴则增大1.4倍,达±0.28%。
82.用肯纳¢16 小刀片(KCM25)切NAK80材料每刀深0.4mm,宽2/3 刀直径,线速度55m/min,0.5mm/rev,风冷,较合适。
83.磨床加工中,0.5mm 的沟槽也能磨出。
84.回位梢的表面只有0.5mm 厚左右是硬的,里面是软的。
85.精加工平面时,STEP 一般采取刀具直径的2/3~4/5,和慢走刀方式。
86.滑块槽的公差为-0.01 和+0.01。
87.设计前,与客户对图面打合(分型面的确定、顶针位置的确定、倒沟的处置方式、浇口位置与形状、肉厚与缩水的关系、公差大小等的进一步的确认)是非常必要的,这对进一了解客户的设计意图、增加设计命中率是非常必要的,这是设计者首先应该树立的观念,设计者不能自作主张。
88.热流道一般适用于量产24 万件以上的塑料模。
89.对于象9029、0031 等采用潜伏式浇口的模具,进胶口的直端部分常采用圆形或扁形,然后,采用圆形或扁形的顶针顶出,但因为顶针小进胶口长,如果进胶口处没有脱模斜度,部品顶出时常会发生顶出不良或把顶针折断的现象,因此,该处应开0.5°~1°的脱模斜度,以便顶出。
90.象Olympus 的cg5375f1 背盖,PC 料、一模一件,一个点浇口的模具,使用住友75 吨成型机注塑时注塑压力达200MPA。
91.流道比较大的模具,起冷料作用的部位也应该相应加长,如象0039 的主流道末端次试模后加长了14mm。
92.大模具在设计时就应该考虑好排气槽的设计,不应该在试模后再指定,根据经验,一般在模具的四周用铣刀或磨床(根据模具精度需要而定),加工出一周的浅槽,深度小于塑料的溢边值。
93.带C 角的入子,如果C 角部位正好与模仁相接,为了防止在部品上出现毛边,其入子底部到C 角处的长度公差应该为+0.05,如图所示:
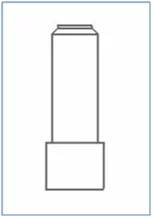
94.放电加工中对一般要求的模具面粗度7um 即可,精密模具中的一般面粗度为4um,象外观要求高的模具面粗度要求达2um。
95.模具材料的订购一般应该比要求的更大尺寸大3~5mm。
96.拉料梢尽量不要采用背面锁螺丝的固定方式,因为该方式会产生应力会使拉料梢易断,比较好的方式是拉料梢能够较自由的活动。
97.线切割一般会在尖角部位产生0.2mm 的R 角,在模具设计中在碰到要求使用线切割的位置(入子孔、方型顶针孔等),一定要考虑此R 的影响,以免产生飞边、毛刺等问题。模具达人微信公众号都是干货!
98.滑块与模仁的贴合部位一般应该设计成单边2-3°的斜度,既可以避免磨损,又便于产生预压。
99.涂装的厚度一般为单边0.02~0.03mm,模具的抛光量一般为单边.02~0.03mm,在产品设计和模具设计的配合尺寸的选取上一定要考虑这一点。
100.钳工在配入子时手法非常重要,入子以能缓缓流动为更佳,入子插入腔中1/4 深度时不能有松动的感觉。
101.在成型镜片、高精度齿轮等精密零件时,为了提高部品的精度,保持模具的高刚性非常重要,为此,除#102、#103 外其它模具零件(材料S45C、S55C)常需热处理到45°HRC;#102、#103 之所以不需热处理,是因为模仁部分常比模板高。
102.成型镜片常需采用YAG-250(粉末冶金钢材、非常纯净、产于大同钢材)的模具材料,热处理到56±1°HRC。
103.有时模具的表面有一些小圆凹点需要抛光,在用常规方法难以解决的前提下,有时采用纤维油石(非常贵),有时采用一种简单的方法,把牙签夹在小摇臂钻上打到6000-10000 转/分钟,用手轻托模仁,沾上钻石膏,把需要抛光部分轻轻去碰牙签来抛光。
104.一般部品的顶针逃肉深为0.1(公差为0~+0.02),精密成形时是0.03(公差为0~+0.01),在这种情况下对顶针固定板(上顶出板)、顶针垫板(下顶出板)及用于固定顶针的逃孔深度、左右两支撑块、可动侧模板、可动侧模仁、顶针本身靠位的长度及其总长度都有非常严格的要求,必须按设计要求严格执行。
105.查看已经成形好的部品的顺序为:表面是否有烧焦,流痕,侧壁是否有拉伤,填充是否充分,分模线、靠破线位置是否有毛边,肉厚处的反面是否有收缩,顶针的反面是否有顶出痕,顶针逃肉深度是否合理。
106.用推板顶出式模具,如果为一模多件,固定侧与可动侧也不宜分成多块,而以采用整体式模仁设计为宜,以便于顶出平衡。
107.对抛光来说#5000~#8000的钻石膏即可以达到镜面效果。
108.绞刀加工的圆跳动为0.05mm。
109.YKMA-0058(大分佳能前盖)螺牙计算步骤:螺压主参数:M41×0.75(螺距P=0.75、大径D=41、中径D2=D-0.649519×P、小径D1=D-1.082532×P、作用高度H1=0.541266×P),部品收缩率为S=1.0058,因此,模仁的螺距p1=0.75×S、大径d1=41×S、中径D2= d1-0.649519×p1、小径D1= d1-1.082532×p1、作用高度H1=0.541266×p1。
中间有一段全英文的,删除了。
136.EP 在模仁内也应逃肉,以减小摩擦力,如图:
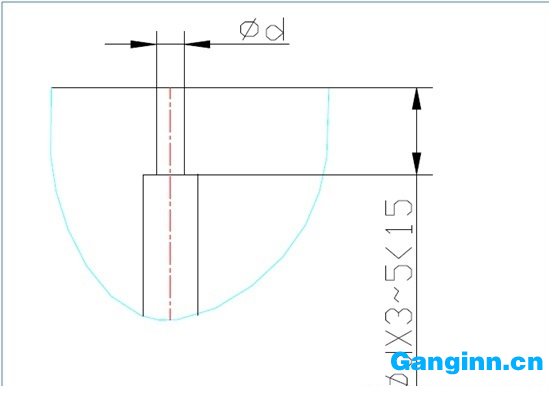
137.小拉杆上弹簧一般选择蓝色(轻载荷)TL 型,以保证弹力足够。
138.拉料销一般选用RLRT 型,保证如下图寸法。101 板上过孔大0.2(双边),不标公差。为了保证同轴度,101 板与101A 板拉料销孔,灌嘴孔组立线割,在开模时(101 与101A 拉开),才不会拉断。
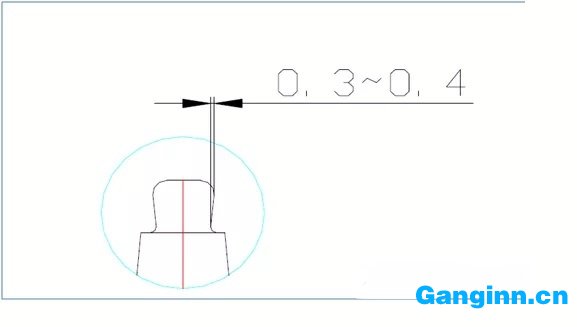
139.如下图标结构为加工时避免逃气不良,常采用以下方式设计。
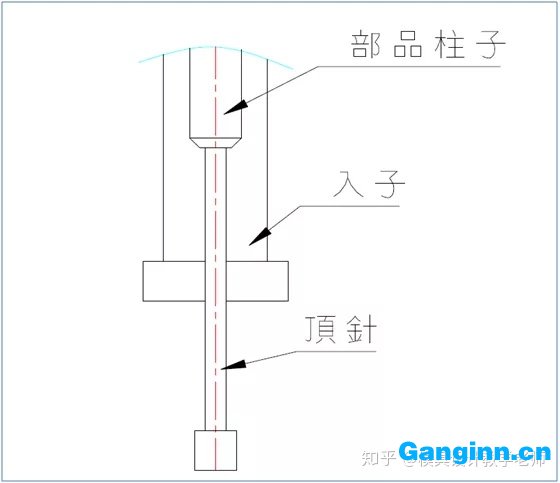
140.加纤等材料对模仁损耗大,一些易磨损部位应尽量采用镶入子。
141.对一模一件大型模具,在不发生干涉又不能对称排列时,支撑柱可以不对称分布,两件以上依情况也可以不对称排列。
142.一组成功的模具,一位的设计者,往往在小的、细节上表现出来。微动开关,型开防止块必要。模具达人微信公众号都是干货!
143.QF-TE:加热(烧入)-回火。
144.成形机成形吨数的选举由成形面积、合模力、模具大小、型帝力决定。
145.点浇口常有以下两种形式,逃肉深B由材料、角度A等因素决定,常为0.5~0.6。ABS、PC材料,逃肉深度稍大些。

146.PPE材料模温60℃左右较合适。LCP 材料成形较好,能成形0.14 厚的塑料制品。如下图部品:
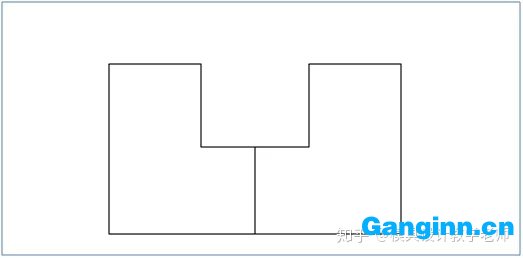
147.三板模型开量:PL1=废料长度(垂直距离)+10 (机械手取)PL1=灌嘴口到浇口长度(相对距离)+15 (自动取下)PL2=A+2~3MM
148.对大部品或部品外观有要求时,常采用模仁冷却,有时模仁与模板同时冷却,甚至滑块、斜销也会开冷却孔。对镜片模冷却回路为井字型。对于一些大型模具,像本体,前后盖,镜筒模具(YKMA-1116),101、101A也开设水孔加热起到维持温度平恒,开模运动顺畅作用。
149..点浇口流道与浇口有一定相关关系。
150..检测时人为误差一般为2umm ,千分尺测定时,接触部品时响3 声为宜,测定温度为22℃+0.5℃。
151.镜面模具一般采用入子顶出形式,大部品其#301 上一个入子需两个拉杆,这样入子顶出不平衡,就容易拉伤入子,特别是巽形入子。如1024,1141,如下图把入子下端逃空,104 板上装上导套,用螺丝把入子与导柱由圆形导向块连接于107 板,在导套内作导向运动,这样量产时会更顺畅。
152.PSF材料不易产生静电,但价格为PC 的2-3 倍,因此产品选用PSF,而一般产品选用PC。
153.如下图1、2 部品,要检测图2 上的凸点高度,做图3示治具,把图2 箭头所示处帖在图3箭头所示处,把治具3 翻转后即可测定。
154.该模具加工的顺序为:
A.凸点先不加工,平面咬花.
B. 然后,检测该平面的平面度,修模直到OK.
C.更后才加工所有的凸点,其中,部品上凸点的高度应比侧面的两条筋低处0.03-0.05mm,这一点应该在打合时向客户提出.
D.再后, 抛光凸点, 抛光时应该在30-50 倍的放大镜下抛.(平时抛光也更好在5 倍的放大镜下抛),抛光前的机加工(用加工中心铣出,而不能用放电,以免凸点大小不均)余量应留0.03mm 左右,供抛光.
155.镜面抛光可达0.05um, 抛光前应该预留0.03,精度要求高时一定预留多一些,以备下次有型修量(用机器抛光要均匀些).
156.潜伏式浇口其浇口应开在斜面上,而不应开在平面上,以防进胶时直接冲击模仁,和在部品上产生焦痕。模具达人微信公众号都是干货!
157.部品浇口处出现焦痕时对策:降低压力,降低注射速度,以便减低材料剪切力。
158.在识部品图时,用涂色或标注面高方式,基准要求尽量统一,基准为0.00,基准以上为“+”,基准以下为“-”,一般图面标注主视图及俯视图即可,但对本体之类复杂图面,应标注6 个面。
159.3 次元测定头有三种:
160.部品很薄的刀口部成形压力大时易碎化,塑料加玻璃纤维时更加容易碎化。
161.在成形如下图部品时,T=2/3t,当有外观(细咬花)时,T=1/2t,部品不易缩水。模具达人微信公众号都是干货!
162.成形如下图部品时,T>2/3t时,外观不易产生光泽,在角度A 越小(30°)或R 时越不易产生光泽,因为这样不会使树脂逆流,形成光泽不一样。
163.如下部品,点浇口分布应满足:流动性好的材料l / t=60~70(甚至100 也行),l 为点浇口至更远处距离,t 为平均肉厚,含玻璃纤维20%时l /t=40~50,不正常肉厚时l / t=40~50。
164.材料流动时,如下图示,材料分两种:结晶性,后收宿大,吸水性强,如镜筒用的POM,PBT,PP,在48H 后测定才稳定﹔非结晶性,如ABS,PC。
165.当3D 寸法公差为单向公差时,应向客户检讨,尽量调为双向公差﹔对大面积肉薄部品为保证成形厚度,采用追加浇口﹔有时表面不能抛太光,特别是作镜面时,会粘住离型不良,#5000 就会发生真空凝质,可再抛粗一些﹔做光学镜片的材料,钢材应含镍15%以上。
166.STAVAX分三级:一般级,MS 级,ES 级(光学用镜面)
167.SKD61分两级:一般级,锻造级,没有方向性,性能好。
168.ZDC2铝纤合金,用于相机三角架螺丝,相机前端交换镜头部分。
169.如下图部品应满足:b=1/4~1/3t﹔a=1/2c,图2 单边凹槽应开在浇口流向的一方,以免直接冲击柱子。
170.模具设计时要考虑机械手的取出空间。
171.架模速度更快为6 秒即全自动架模,一台注模机20 万。(采用模具预先加热水孔,设计时水孔连接好,架模时只留进出水口中。台湾架模速度为3 分钟左右。
172.型内切断浇口,光学部件使用较多。
173.流道与品质关系:(特别是成形镜片时)
174.型强度计算应考虑:成形锁模力,模板强度,模仁强度等。
175.镶件可用真空吸引。
176.压力感知器,用于检测模具内部压力损失,有时设计在顶针的末端(对小部品)。对大部品有时可以直接放在模腔内。
177.日本的成形机更多可以设定10级参数(压力,注射速度质量较好的成形机参数设好后一般不会漂移。
178.成形机灌头与模具接触压力为6 吨左右,45 吨以下为3 吨左右。
179.增加铍铜硬度可镀硬铬,一般浇注成形。
180.喷砂材料有:玻璃砂,氧化铝,核桃粉,铁砂。
181.玻璃丸粒度:#200,#150,#400(象牛奶粉)。
182.成形材料与模具间成形量关系:
NAK-80 用于产量少的模具。G:玻璃纤维C:碳纤维
183.事务机(大部品),采用热浇道好,模具内有加热系统。热浇道分三种:全热浇道,半热浇道,半半热浇道。
184.如下图:
185.隔热板用在成型机上,位于模具的前后,采用玻璃纤维板或电木,前者价格为后者的5倍,用于模温高,光学部品,碳纤维20%以上的模具。
186.SLIDE后退是因为阻挡块太小,再做一个类似阻挡块来解决,或把楔紧块前端加工尖一些。
187.模具的冷却方式有:水、冷冻水(-5℃)、油、电热棒。
188.更小能线割0.14 孔,深1MM,用Φ0.03 线来线割,穿线孔用LASER 加工,化学腐蚀更小可加工Φ0.4 孔。
189.扁顶针易跑毛边,易卡死,尽量少用。一般作0.5 及以上较好。0.5 以下其有效距离<10。模具达人微信公众号都是干货!
190.温度感知器分K(CA)TYPE CI TYPE 其原理:
史上更全模具术语中英对照,不是更全你打我!
191.如果入子不运动,t 更低可取0.2mm,如果入子运动,t为0.5~0.7mm(0.6mm).
192.常用钢材及其硬度适用范围:
193.常用塑料材料缩水率:
194.部品上字凸,模仁上字凹,加工时用刀直接刻﹔部品上字凹,模仁上字凸,加工时用电极放电加工完成。如下图部品,要求有字部位亮一些,首先把字放电加工OK 后,抛光到所需之亮度,再把整个面放电加工,但放电时要把已加工好的字的部位在电极上避空。如果表面有外观要求,应先咬花处理等,再加工字。
195.镜片模其流道一般采用圆形,固定侧、可动侧各一半,拉料销形状如下图
196.在二板模中,当主流道长度>60时,可采用无灌嘴形式,即把固定侧模仁做成灌嘴状,101板从定位环处作成圆锥孔,成型时,直接进入201 灌嘴口。
197.在加工滚筒时,如下图示:固定侧模仁与可动侧模仁先磨斜面,其垂直度能保证(5umm内),再用螺丝锁紧两块模仁,磨平面(用肉眼看上去贴合线不易看见),然后线割孔。
198.设计齿轮时,注意部品放置方向,如图示:外齿轮部品,模仁上线割线留在箭头所示处为宜。
199.线割入子倒角处可为R 角,也可为直角,线割内孔时倒角处必为R 角,在配模时可为R 角相配,也可把内孔倒角处清角配模,具体依实际情况而定。
200.PT1/4*15[%%C10]其1/4 指螺纹孔径为13.5,1/8 指螺纹孔径为9.6。
201.如图示冷料穴,能抓紧废料,加工时用车刀加工,
202.塑料部品或冲压部品其表面常需印刷字,但怎样检测其粘着的牢固程度,方法有:
A用常用的有机溶剂、汽油,或酒精擦洗。
B用强胶带粘在上面,然后迅速撕起。
203.对入子多、结构复杂的模具成型10000 次,(约一星期左右需保养一次),简单件则要50000次,(约10 天左右保养一次)。对塑料模来讲,作动部位的保养上油十分重要,因为长期的成形中会形成大量瓦斯气,附在模具上,影响动作的顺畅。
204.粗外观电极抛光为#800 砂纸,中外观电极抛光为#1200 砂纸,细外观电极抛光为#1500~#2000 砂纸。
205.抛光时用火花油或煤油作抛光液,以免粉未粘在工件上和砂纸上,抛完后用去污水清洗。
206.测量部品时至少检测3 模才准确,对本体检测时台湾测定5 模,每模约3 天测完。
207.对图面上不能检测的寸法,应向客户提出,由组立判定。
208.电镀:ABS+CU+Ni+Cr,其中CU 厚20UMM,Ni 厚10 UMM,Cr5 UMM。
209.蒸眷:镀金0.3UMM~0.4UMM(纯金) 。
210.部品挂钩处更好R,与客户检讨,以免部品易折断。
211.如下图,磨床加工时,同轴度,直径易保证,但此处两个寸法不易保证。
212.磨床分类:GC 内外圆磨,JG(GN)圆筒研磨加工,GF、GS 平面磨床,GP(profile)投影磨床。
213.热处理目前一般预留0.20mm。(YORKEY 更低使用过预留0.04mm, 一般预留0.10mm)有时电气炉代替真空热处理,但其表面会脱碳,变黑。
214.非球面加工机:0.1UMM,800 万台币﹔0.01 UMM,1200万台币﹔0.002 UMM,2000 万台币。(地板防震)
215.对模板、模仁要求:c//d0.005(一般光学),0.002(特殊光学),六面垂直度平行度0.002MM以下(光学模具),可以采取中间逃肉2mm 深来实现,如下图:
216.亚光测试加工极限:0.3UMM,在制作特殊光学时,应尽量采用磨床加工保证其加工精度。
217.镜筒模具模坐标准:350X350﹔400X400。
218.在选择注射机时,除了保证注射机能套入,还要计算模具总的射出重量<注射机射出重量。
219.光学分三类:窗类﹔一般光学﹔特殊光学。光学单位:本(日本名词) 条(牛顿环、亚斯:T/2),环数越多,部品越差,环数越少,部品越佳,如下图:5 本指5 条环,实际值=测量数/2,检测部品用原器或雷射干涉仪。
220.原器分:原原器(1 个):测定原器用﹔原器:测定模仁用﹔次原器:检测模仁加工用。
221.对窗类镜片P.L 面作在上表面下0.1~0.2 处,如下图示
222.特殊光学镜片如下图:刻线在模仁上加工用钻石刀,此线看起来模糊有两种原因:一是成形充填不足,二是加工不是尖角,为一小平面:(箭头所示)

225.加工球面SR0.1MM,进刀1UMM,2 UMM 。
226.模仁公差为部品公差1/5,电极公差为模仁公差1/2。
227.在测定小R,如R0.14,R0.002,用电子显微镜放大500 倍测定。放大倍数达50000 倍时,冷氯关闭,自动检测。
228.逃气如下图寸法,流道及部品图所示处先作逃气。
229.当在加工角度公差30’以下时,要设计加工治具加工,必须采用平面磨床加工才可达到要求。
230.图面表示符号:
免费获取报价
原文标题:塑胶模具设计经验及注意事项大全及使用材料
本文部分内容来源于网络,我们仅作为信息分享。本站仅提供信息存储空间服务,不拥有所有权,不承担相关法律责任。如发现本站有涉嫌抄袭侵权/违法违规的内容,请发送邮件至tokaits@163.com举报,一经查实,本站将立刻删除。
上一篇:热处理的四个技术处理阶段